Non Destructive Testing (NDT) COURSES
NDT
ASNT LEVEL-II
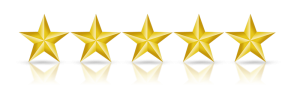
Duration : 1 Month
Certified Trainer
Dedicated Career Services
Unlimited Interviews
APPLY NOW
QUALITY CONTROL
ENGINEERING(QA/QC)
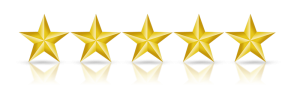
Duration : 1 Month
Certified Trainer
Dedicated Career Services
Unlimited Interviews
APPLY NOW
CERTIFIED
PIPING ENGINEER
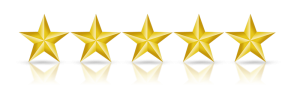
Duration : 1 Month
Certified Trainer
Dedicated Career Services
Unlimited Interviews
APPLY NOW
ADVANCED DIPLOMA IN
OIL&GAS PIPING
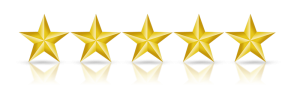
Duration : 2 Months
Certified Trainer
Dedicated Career Services
Unlimited Interviews
APPLY NOW
PG DIPLOMA IN
PIPING & PIPELINE ENGINEERING
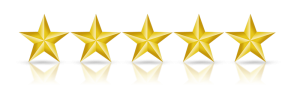
Duration : 3 Months
Certified Trainer
Dedicated Career Services
Unlimited Interviews
APPLY NOW
POST GRADUATE DIPLOMA IN
OIL&GAS
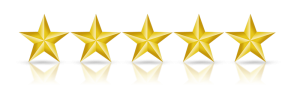
Duration : 3 Months
Certified Trainer
Dedicated Career Services
Unlimited Interviews
APPLY NOW
ADVANCED PG DIPLOMA IN
OIL&GAS PLANT
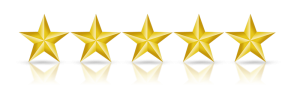
Duration : 6 Months
Certified Trainer
Dedicated Career Services
Unlimited Interviews
APPLY NOW
Non Destructive Testing(NDT) TRAINING
Looking for Best Non Destructive Testing Training in Chennai, EGAI is No 1 NDT training institutes in Chennai offering professional training by experts. Call +91-9176-604201, +91-7305-356204.
NDT Training course, we believe in practice what you preach and therefore each candidate is encouraged to practically conduct each topic that is discussed for better understanding of real-world scenario Non Destructive Testing. This practice of comprehensive training allows candidate to gain all the concepts and skills effectively and to later efficiently apply on their field of work.
EGAI is one of the Best NDT training institute in Chennai with 100% placement assistance. EGAI has well structure modules and training program designed for both students and working professionals separately. At EGAI, NDT training is conducted during all 5 days, and special weekend classes. Can also be arranged and scheduled. We also provide fast track training programs for students and professionals looking to upgrade themselves instantly.
Why Non Destructive Testing(NDT) Training in Chennai at EGAI?
Learning evergreen technology from EGAI makes your career to be rich one. Our NDT courses include all recent technologies like OIL and GAS, PIPING Engineering and etc. EGAI is home to practical, real-time and placement assistance focused training in Chennai. Our Non Destructive Testing NDT Training is carried by experienced trainers based on the industry standards and training students for real world challenges.
What Is Nondestructive Testing?
Nondestructive Testing (NDT) plays an important role in assuring that structural and mechanical components perform their function in a safe, reliable, and cost-effective manner. NDT technicians perform the necessary tests to locate the indicators and discontinuities that may cause failures or shut downs in such systems. These tests are performed in a manner that does not affect the future usefulness of the object or material – hence, the name “nondestructive”. NDT allows for careful and thorough materials evaluation without the need for deconstruction or damage. NDT is typically used at various points in a part’s life cycle. NDT can be used prior to the use of a component for the sake of quality control. NDT is also employed while components are in use to detect service related conditions caused by wear, fatigue, corrosion, stress, or other factors which affect reliability.
ASNT NDT L-I & L-II CERTIFICATION COURSES :
VISUAL TESTING
“Visual inspection is the process of examination and evaluation of systems and components by use of human sensory systems aided only by mechanical enhancements to sensory input such as magnifiers, dental picks, stethoscopes, and the like. The inspection process may be done using such behaviors as looking, listening, feeling, smelling, shaking, and twisting.
“It includes a cognitive component wherein observations are correlated with knowledge of structure and with descriptions and diagrams from service literature.”
Visual testing (VT) is the oldest and most common nondestructive testing (NDT) techniques. It is typically the first step in the examination process to inspect a variety of product forms including castings, forgings, machined components and weld elements.
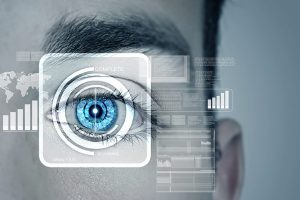
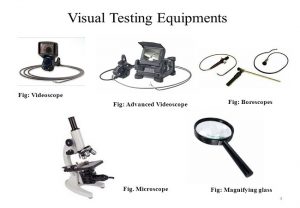
Magnetic Particle Testing
Magnetic Particle Testing (MPT), also referred to as Magnetic Particle Inspection, is a nondestructive examination (NDE) technique used to detect surface and slightly subsurface flaws in most ferromagnetic materials such as iron, nickel, and cobalt, and some of their alloys. Because it does not necessitate the degree of surface preparation required by other nondestructive test methods, conducting MPT is relatively fast and easy. This has made it one of the more commonly utilized NDE techniques.
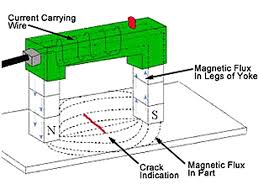
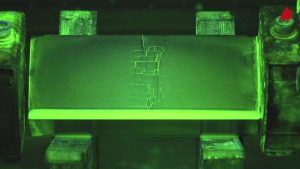
Dye Penetrant Inspection
Dye penetrant inspection (DP), also called liquid penetrate inspection (LPI) or penetrant testing (PT), is a widely applied and low-cost inspection method used to check surface-breaking defects in all non-porous materials (metals, plastics, or ceramics). The penetrant may be applied to all non-ferrous materials and ferrous materials, although for ferrous components magnetic-particle inspection is often used instead for its subsurface detection capability. LPI is used to detect casting, forging and welding surface defects such as hairline cracks, surface porosity, leaks in new products, and fatigue cracks on in-service components.
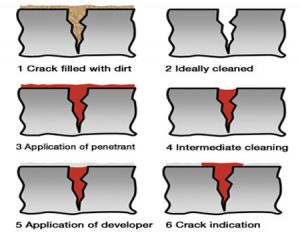
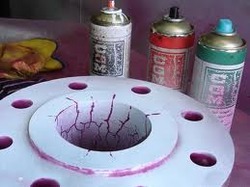
Radiographic Testing
Radiographic Testing (RT) is a nondestructive testing (NDT) technique that involves the use of either x-rays or gamma rays to view the internal structure of a component. In the petrochemical industry, RT is often used to inspect machinery, such as pressure vessels and valves, to detect for flaws. RT is also used to inspect weld repairs.
Compared to other NDT techniques, radiography has several advantages. It is highly reproducible, can be used on a variety of materials, and the data gathered can be stored for later analysis. Radiography is an effective tool that requires very little surface preparation. Moreover, many radiographic systems are portable, which allows for use in the field and at elevated positions.
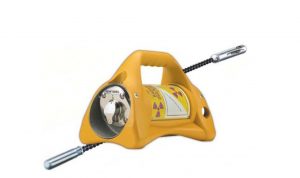
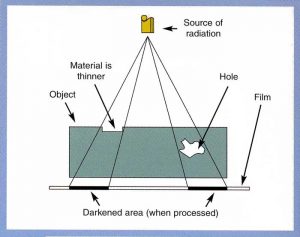
ULTRASONIC TESTING
Ultrasonic inspection (UT) is a non-destructive test method that utilizes sound waves to detect cracks and defects in parts and materials. It can also be used to determine a material’s thickness, such as measuring the wall thickness of a pipe. Because of the portability of the equipment and variety of methods available, ultrasonic testing allows for inspection of parts that are large, irregularly shaped, or unable to be transported.
Ultrasonic inspection relies on electronic transducers that transmit high-frequency sound waves to a material. These sound waves bounce back crystal-clear images, which reveal key characteristics about a material’s properties. The images created by ultrasonic testing can indicate cracks, weld grooves and fractures, as well as indicate material thickness and outline moving components.
Because this method has higher power potential than other non-destructive test types, ultrasonic inspection can produce images that are more clearly defined than other methods, and indicate characteristics deeper than surface level. Depending upon the test requirements, parts can be tested by immersion (in-lab testing) or contact (portable/in-air) inspection.
Ultrasonic testing is often used in situations where radiographic inspection is not possible, because it requires access to only one side of the test specimen.
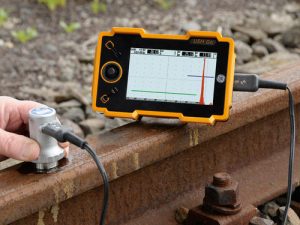
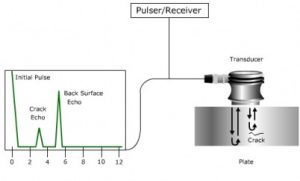
Radiograph Film Interpretation
In addition to producing high quality radiographs, the radiographer must also be skilled in radiographic interpretation. Interpretation of radiographs takes place in three basic steps: (1) detection, (2) interpretation, and (3) evaluation. All of these steps make use of the radiographer’s visual acuity. Visual acuity is the ability to resolve a spatial pattern in an image. The ability of an individual to detect discontinuities in radiography is also affected by the lighting condition in the place of viewing, and the experience level for recognizing various features in the image. The following material was developed to help students develop an understanding of the types of defects found in weldments and how they appear in a radiograph.
Discontinuities
Discontinuities are interruptions in the typical structure of a material. These interruptions may occur in the base metal, weld material or “heat affected” zones. Discontinuities, which do not meet the requirements of the codes or specifications used to invoke and control an inspection, are referred to as defects.
Phased Array Ultrasonic Testing
Construction and power generation sectors of the industrial sector widely use the phased array model of ultrasonic testing. The phased array probe method is an advanced non-destructive testing (NDT) method that can be used for detecting cracks and flaws which eventually determines component quality. Phased array probe method of testing provides control over parameters such as beam angle and focal distance. As a result, this method is very efficient in defect detection and speed of testing.
Apart from flaw detection, the phased array model of ultrasonic testing can also be used for corrosion testing and measurements pertaining to wall thickness. In a broader perspective, phased array can be used for the following industrial purposes:
- It can be used for inspection of welds.
- As mentioned above, this method can also be used for thickness measurements.
- Corrosion inspection.
- Flaw detection is the primary application of phase array model of ultrasonic testing in industries.
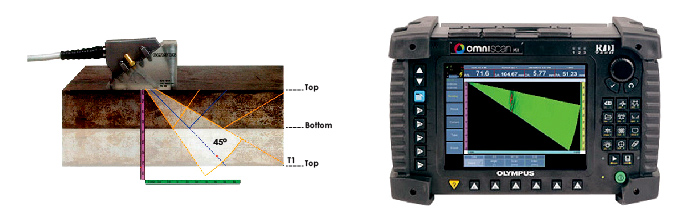
EDDY CURRENT TESTING
In eddy current testing, a coil carrying an AC current is placed close to the specimen surface, or around the specimen. The current in the coil generates circulating eddy currents in the specimen close to the surface and these in turn affect the current in the coil by mutual induction. Flaws and material variations in the specimen affect the strength of the eddy currents.
The presence of flaws etc is therefore measured by electrical changes in the exciting coil. Both voltage and phase changes can be measured, but some simpler instruments measure only the voltage changes.
The strength of the eddy currents produced depends on the:
a) electrical conductivity of the specimen;
b) magnetic permeability (for a ferromagnetic specimen);
c) stand-off distance between the specimen and coil;
d) AC frequency used in the exciting coil;
e) dimensions of the coil and specimen;
as well as the presence of flaws, and much of the success of eddy current testing depends on separating the effects of these variables. Most eddy current instruments require calibration on a set of test specimens and the flaw sensitivity can be very high.
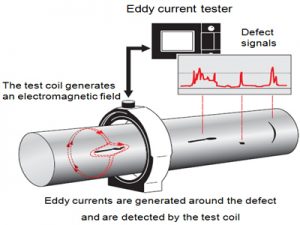
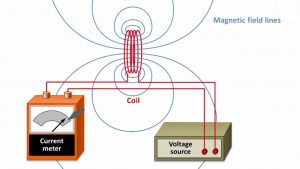
Computed Tomography Testing
Computed Tomography (CT) is a powerful nondestructive evaluation (NDE) technique for producing 2-D and 3-D cross-sectional images of an object from flat X-ray images. Characteristics of the internal structure of an object such as dimensions, shape, internal defects, and density are readily available from CT images. Shown below is a schematic of a CT system. The test component is placed on a turntable stage that is between a radiation source and an imaging system. The turntable and the imaging system are connected to a computer so that x-ray images collected can be correlated to the position of the test component. The imaging system produces a 2-dimensional shadowgraph image of the specimen just like a film radiograph. Specialized computer software makes it possible to produce cross-sectional images of the test component as if it was being sliced.
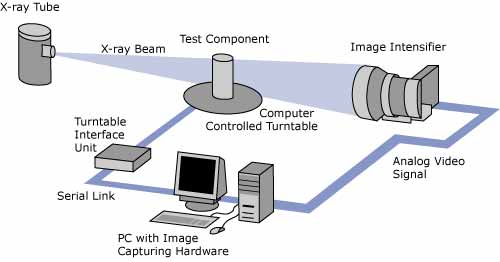